Advanced Houston Welding Inspection Techniques for Accurate Outcomes
Advanced Houston Welding Inspection Techniques for Accurate Outcomes
Blog Article
How Welding Evaluation Works: An In-Depth Analysis of Techniques, Standard, and the Role of Assessors in Ensuring Structural Stability and Safety
Welding inspection is a crucial part in the construction and manufacturing sectors, where the stability of welded joints is paramount to security and dependability. Assessors are tasked with not just assessing weld top quality versus rigid criteria but also translating complicated codes and criteria.
Importance of Welding Examination
Welding inspection is vital in making sure the stability and safety of welded frameworks, with research studies suggesting that approximately 70% of architectural failings can be traced back to inadequate welding practices. This highlights the relevance of organized evaluation procedures throughout the welding lifecycle, from prep work to completion. Reliable examination not just identifies problems prior to they rise into substantial concerns however also makes certain conformity with sector requirements and guidelines.

The function of welding inspectors prolongs beyond plain quality control; they are essential in safeguarding public safety and security and reducing responsibility for organizations. By executing rigorous assessment protocols, business can identify problems such as insufficient combination, splits, or excessive porosity, which can jeopardize the general strength of a welded joint. Moreover, continuous training and certification of examiners contribute to the total high quality assurance in welding operations, cultivating a culture of safety and security and quality.
Furthermore, welding evaluation plays an essential role in preserving functional performance. Identifying problems early at the same time facilitates prompt restorative activities, decreasing expensive rework and job delays. Ultimately, a robust inspection structure functions as a structure for durable and reliable welded frameworks, guaranteeing they fulfill both useful and safety needs.
Common Examination Approaches
Exactly how can one guarantee the high quality of welded joints throughout the evaluation process? The implementation of various inspection approaches is crucial in assessing weld integrity and recognizing prospective defects. Typical approaches consist of Visual Examination (VT), which is usually the initial line of defense, allowing inspectors to identify surface area problems such as fractures, porosity, or incomplete blend by aesthetically evaluating the welds.
Ultrasonic Evaluating (UT) is one more widely used strategy, utilizing high-frequency acoustic waves to recognize internal issues within the weld. This method is especially effective for detecting problems that are not noticeable to the nude eye. Radiographic Testing (RT) uses X-rays or gamma rays to produce photos of the weld, making it possible for the identification of volumetric defects, such as additions or voids.
Magnetic Particle Evaluating (MT) and Fluid Penetrant Evaluating (PT) are additionally popular methods, concentrating on surface area issues. MT counts on magnetic fields to reveal surface and near-surface discontinuities, while PT entails using a fluid dye to highlight imperfections. Each of these approaches serves a distinctive purpose, making sure the comprehensive analysis of welded joints and safeguarding architectural honesty and security.
Standards for Examining Welds
The evaluation of welds is guided by a set of well established requirements that guarantee both performance and safety and security in welded frameworks. These requirements incorporate different elements, including weld dimension, account, and infiltration, which have to conform to specified criteria. Conformity with market codes, such as those set by the American Welding Society (AWS) or the American Culture of Mechanical Designers (ASME), is crucial in figuring out the reputation of a weld.
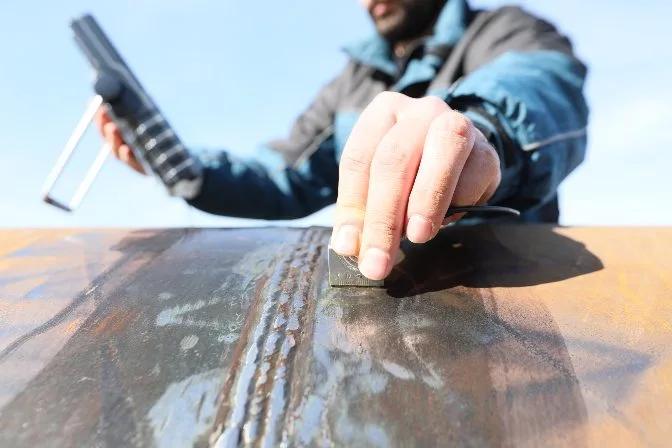
Weld metallurgy plays a vital role; the assessment thinks about the fusion high quality in between base and filler products, along with heat-affected zones. The overall mechanical residential properties, including tensile strength and ductility, have to meet the requirements developed for the particular application. Collectively, these criteria make sure that welds not only meet visual requirements however also execute reliably under functional conditions.
Role of Welding Inspectors
A welding inspector's know-how is pivotal in making certain the honesty and high quality of bonded frameworks. These experts play a vital role in the construction and building and construction procedure by verifying that welding operations comply with established standards and requirements. Their responsibilities include a thorough variety of jobs, including visual examination of welds, examining welding documentation, and carrying out non-destructive testing (NDT) approaches such as ultrasonic or radiographic testing to determine defects.
Welding inspectors are likewise in charge of interpreting welding codes and requirements, guaranteeing that the welders are qualified and that the materials utilized fulfill the essential requirements - Houston Welding Inspection. They have to preserve careful documents of assessments, which function as documents of conformity and quality control. These assessors frequently work together with engineers and job supervisors to address any kind of problems that emerge during the welding process, supplying referrals for restorative actions when needed.
In addition to technical abilities, reliable communication is vital, as welding inspectors must communicate findings clearly to stakeholders and facilitate training and guidance for welders. Ultimately, their role is indispensable to maintaining safety and security and reliability in bonded frameworks, contributing substantially to the total success of building jobs.
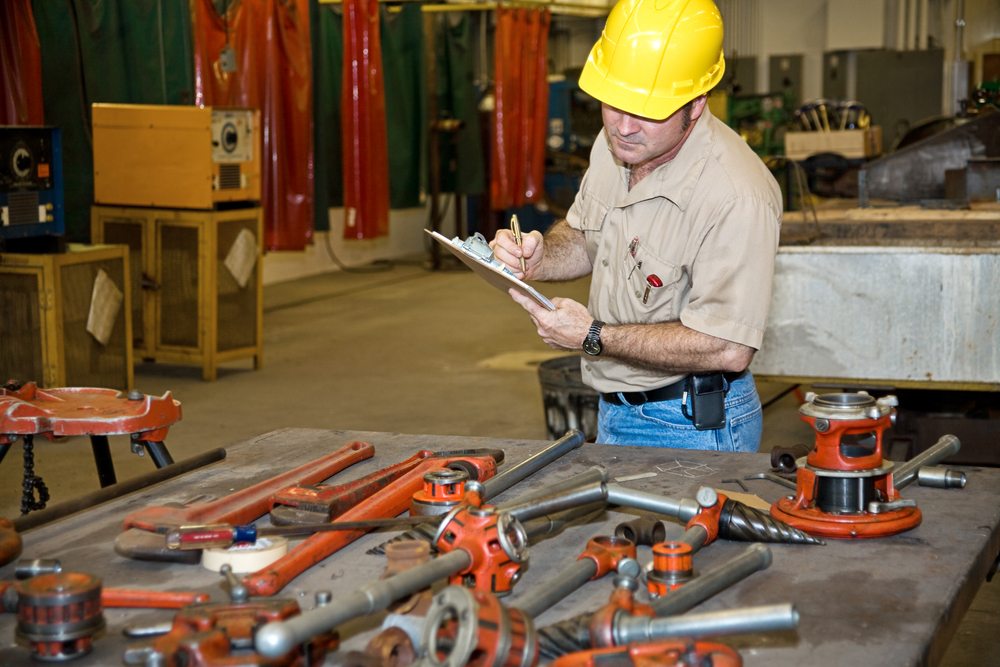
Obstacles in Welding Inspection
What challenges do welding examiners deal with in their vital role? The complexities of modern welding strategies and products existing substantial obstacles for examiners tasked with guaranteeing compliance with security standards and structural stability. One main recommended you read obstacle is the Related Site quick advancement of welding technology; examiners need to continually upgrade their expertise and abilities to remain reliable. This recurring education and learning is important to comprehending brand-new products and procedures, which can vary commonly in qualities and demands.
Additionally, examiners commonly come across variants in worksite conditions that can impede assessment procedures. Variables such as environmental problems, availability, and the physical state of the welded frameworks can complicate comprehensive analyses. Time restraints imposed by task routines can further pressure assessors, potentially influencing the thoroughness of their analyses.
In addition, the subjective nature of some inspection methods can lead to variances in assessments. Aesthetic assessments might differ based on the examiner's experience and point of view.
Conclusion
Welding examination is crucial for preserving architectural honesty and security in numerous sectors. Inevitably, efficient welding assessment contributes substantially to mitigating threats and enhancing the general integrity of bonded frameworks.
Welding inspection is a vital component in the building and manufacturing sectors, where the stability of welded joints is paramount to security and integrity.Welding inspection is essential in making sure the stability and security of welded structures, with researches showing that up to 70% of structural failures can be traced back to poor welding techniques. Their duties encompass a detailed variety of tasks, consisting of aesthetic assessment of welds, assessing welding documents, and performing non-destructive screening (NDT) techniques such as radiographic or ultrasonic screening to determine defects.
Welding inspectors are likewise liable for analyzing welding codes and requirements, making sure that the welders are qualified and that the materials used fulfill the needed demands. go to these guys Ultimately, effective welding inspection adds significantly to mitigating dangers and enhancing the overall dependability of bonded structures.
Report this page